The same properties that qualify tool steels for tools and dies are also used for other parts that require resistance to wear, stability during heat treatment, strength at high temperatures, or toughness. Tool steels are increasingly being used for mechanical parts to reduce size or weight, or to resist wear or high-temperature shock.
Tool steels are metallurgically "clean," high-alloy steels that are melted in relatively small heats in electric furnaces and produced with careful attention to homogeneity. They can be further refined by argon/oxygen decarburization (AOD), vacuum methods, or electroslag refining (ESR). As a result, tool steels are often specified for critical high-strength or wear-resistant applications. Because of their high alloy content, tool steels must be rolled or forged with care to produce satisfactory bar products.
To develop their best properties, tool steels are always heat treated. Because the parts may distort during heat treatment, precision parts should be semifinished, heat treated, then finished. Severe distortion is most likely to occur during liquid quenching, so an alloy should be selected that provides the needed mechanical properties with the least severe quench.
Tool steels are classified into several broad groups, some of which are further divided into subgroups according to alloy composition, hardenability, or mechanical similarities. |
Hot Work Steel are required for chipless shaping of ferrous and non-ferrous metals and their alloys.the hot material can be formed by applying high pressures or by pouring into a prepared mould. For the various tools required, We supply hot work tools steel which withstand the variable stresses overa long time, thus ensuring great economy.
The following typical properties are essential for a hot work tool steel
High retention to tempering
High hot tensile strength
High hot toughnessHigh wear-resistance
High resistance to thermal shocks
The service properties necessary for hot work tool steel are obtained and adjusted to the intended applications by properlly balancing the alloyingelements silicon, manganese, tungsten, vanadium, cobalt, chromium, nickel, molybdenum and while also taking carbon content into consideration. The most important groups of hot work tool steel are based on chromium-molybdenum or chrome tungsten alloys respectively, with vanadium, cobalt and nickle added for the improvement of specific properties
|
LIST OF GRADES |
CHEMICAL COMPOSITION |
AISI/SAE |
DIN |
W.Nr |
JIS |
|
C |
Si |
Cr |
Mo |
Ni |
V |
W |
Co |
Ti |
H11 |
X38CrMoV51 |
1.2343 |
|
0.38 |
1 |
5.3 |
1.3 |
|
0.4 |
|
|
|
H13 |
X40CrMoV51 |
1.2344 |
|
0.4 |
1 |
5.3 |
1.4 |
|
1 |
|
|
|
H10 |
X32CrMoV33 |
1.2365 |
|
0.32 |
|
3 |
2.8 |
|
0.5 |
|
|
|
|
X38CrMoV53 |
1.2367 |
|
0.37 |
|
5 |
3 |
|
0.6 |
|
|
|
H21 |
X30WCrV93 |
1.2581 |
|
0.3 |
|
2.6 |
|
|
0.4 |
8.5 |
|
|
H12 |
X37CrMoW51 |
1.2606 |
|
0.36 |
1 |
5.3 |
1.5 |
|
0.3 |
1.3 |
|
|
6F2 |
55NiCrMoV6 |
1.2713 |
|
0.55 |
|
0.7 |
0.3 |
1.7 |
0.1 |
|
|
|
6F3 |
55NiCrMoV7 |
1.2714 |
|
0.56 |
|
1.1 |
0.5 |
1.7 |
0.1 |
|
|
|
|
55CrNiMoV424 |
1.2742 |
|
0.56 |
|
1 |
0.4 |
0.5 |
0.1 |
|
|
|
|
57NiCrMoV77 |
1.2744 |
|
0.57 |
|
1.1 |
0.8 |
1.7 |
0.1 |
|
|
|
|
X2NiCoMoTi1288 |
1.2799 |
|
0.02 |
|
|
8 |
12 |
|
|
8 |
0.5 |
H10A |
X32CrMoCoV333 |
1.2885 |
|
0.32 |
|
3 |
2.8 |
|
0.5 |
|
3 |
|
|
Plastic Moulds |
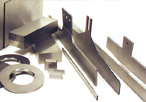 |
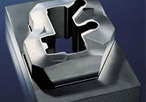 |
Increasing demands for tools in plastic moulding require the specific development of tool steel which have certain service properties for different ranges of application
Tools for the prosessiong of plastic are mainly stressed with regard to pressure and wear.According to the type of plastic, there may in addition exist a stressing by corrosion.
The various types of plastic and different processing methods put certain requirements on the tool stee
lEconomic machinability or cold -hobbing ability
Dimensional stability on heat treatment
Good polishability
Great compressive strength
High wear resistance
Sufficient corrosion resistance |
LIST OF GRADES |
CHEMICAL COMPOSITION |
AISI/SAE |
DIN |
W.Nr |
JIS |
|
C |
Si |
Mn |
Cr |
Mo |
Ni |
V |
Co |
Ti |
Al |
|
|
|
|
|
|
|
|
|
|
|
|
|
|
Case Hardning Steel |
|
|
|
|
|
|
|
|
|
|
|
|
P2 |
21MnCr5 |
1.2162 |
|
0.21 |
|
1.3 |
1.2 |
|
|
|
|
|
|
P4 |
X6CrMo4 |
1.2341 |
|
0.04 |
|
|
3.8 |
0.5 |
|
|
|
|
|
P21 |
X19NiCrMo4 |
1.2764 |
|
0.19 |
|
|
1.3 |
0.2 |
4.1 |
|
|
|
|
|
|
|
|
|
|
|
|
|
|
|
|
|
|
Heat-treated Steel |
|
|
|
|
|
|
|
|
|
|
|
|
P20 |
40CrMnMo7 |
1.2311 |
|
0.4 |
|
1.5 |
1.9 |
0.2 |
|
|
|
|
|
P20+S |
40CrMnMoS86 |
1.2312 |
|
0.4 |
|
1.5 |
1.9 |
0.2 |
|
|
|
|
|
|
54NiCrMoV6 |
1.2711 |
|
0.55 |
|
0.7 |
0.7 |
0.3 |
1.7 |
0.1 |
|
|
|
P20+Ni |
40CrMnNiMo864 |
1.2738 |
|
0.4 |
|
1.5 |
1.9 |
0.2 |
1 |
|
|
|
|
|
|
|
|
|
|
|
|
|
|
|
|
|
|
Corrosion-resistant steel |
|
|
|
|
|
|
|
|
|
|
|
|
420 |
X42Cr13 |
1.2083 |
|
0.42 |
|
|
13 |
|
|
|
|
|
|
|
X36CrMo17 |
1.2316 |
|
0.36 |
|
|
16 |
1.2 |
|
|
|
|
|
|
X30CrMnS17 |
1.2394 |
|
0.3 |
|
1 |
16 |
0.3 |
|
|
|
|
|
|
|
|
|
|
|
|
|
|
|
|
|
|
|
Through-hardening steel |
|
|
|
|
|
|
|
|
|
|
|
|
H11 |
X38CrMoV51 |
1.2343 |
|
0.38 |
1 |
|
5.3 |
1.3 |
|
0.4 |
|
|
|
D2 |
X155CrVMo1211 |
1.2379 |
|
1.55 |
|
|
12 |
0.7 |
|
1 |
|
|
|
|
X45NiCrMo4 |
1.2767 |
|
0.45 |
|
|
1.4 |
0.3 |
4 |
|
|
|
|
2842 |
90MnCrV8 |
1.2842 |
|
0.9 |
|
2 |
0.4 |
|
|
0.1 |
|
|
|
|
|
|
|
|
|
|
|
|
|
|
|
|
|
Nitriding steel |
|
|
|
|
|
|
|
|
|
|
|
|
4340 |
31CrMoV9 |
1.2307 |
|
0.31 |
|
|
2.4 |
0.2 |
|
0.2 |
|
|
|
|
15CrMoV59 |
1.2391 |
|
0.15 |
|
1 |
1.4 |
0.9 |
|
0.3 |
|
|
|
|
34CrAlNi7 |
1.2891 |
|
0.35 |
|
|
1.7 |
0.2 |
1 |
|
|
|
1 |
Maraging steel |
|
|
|
|
|
|
|
|
|
|
|
|
|
X3NiCoMoTi1895 |
1.2709 |
|
0.03 |
|
|
|
5 |
18 |
|
10 |
1 |
|
|
|
|
|
|
|
|
|
|
|
|
|
|
|
Steel for mould frames |
|
|
|
|
|
|
|
|
|
|
|
|
1045 |
C45W |
1.173 |
|
0.45 |
0.3 |
0.7 |
|
|
|
|
|
|
|
|
|